Company
Effect of Cooling Intensity on Al-alloy Precision Casting
Posted: 2015-06-15 04:11:13 Hits: 1938
With the development of casting technology, the mold of modern precision casting is integrated. Consumption of cooling water is high when using old mold casting, because water supply of old mold isn't closed, part of cooling water cannot cool down, besides the intensity of the first cooling and the second cooling is different a lot, producing some casting defects inevitably. However, consumption of cooling water is low with modern mould casting and practice shows that it is only about 70% of the water old mold uses. Now most apply low liquid level casting mold, with the purpose to improve the cooling intensity, reduce or eliminate heating phenomenon in the air gap after the first cooling.
Requirements of cold punching strength for temperature of cooling water cannot be ignored. In general, temperature of cooling water is set at 20 degree, but due to regional climate conditions, facilities conditions of water supply and different temperature of plant lead to great changes, thus regional or seasonal defects of ingot quality occur. Modern mold water supply system has pulse or cross disguised function, which is totally determined by program process, so the cooling intensity can be set to curve based on the requirements of casting technique, especially for some hard al-alloy with poor low temperature plasticity, when precision casting, cold crack and thermal crack exist almost at the same time. Append water retaining plate system, making temperature of the ingot surface rise to the plastic tensile deformation temperature, eliminate cold crack of the ingot and take measures to prevent thermal cracks, thus high-quality ingot will be obtained.
Cooling intensity is also known as cooling rate. Cooling strength not only has influence on the crack of precision casting, but also has greater influence on the organization of the ingot. With the increase of cooling intensity, casting speed increases, the structure of mold is more refined and ingot casting liquid cavity becomes shallower. The size of transition zone narrows, improving the condition of metal feeding, which reduces or eliminates defects such as loose and porosity in the casting and improves density of ingot casting. It also can refine the size of one-time compounds, thus reduce the degree of regional segregation.
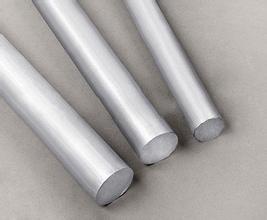